10 Parts Of Hydraulic Pump + PDF & Function
페이지 정보

본문
The piston on this pump is mounted radially inside the cylinder block. The pistons reciprocate perpendicularly to the axis of the shaft. Relying on how the pintle or one-approach valves are organized, these may also be classified. There are variable and fastened displacements out there for radial piston pumps. Inspecting a hydraulic system frequently and performing repairs as wanted will guarantee that each one parts work in coordination. Seek the advice of a technician for upkeep solutions. To seek out out if there's a problem, examine the manufacturer’s instructions. The necessity for hydraulic preventive upkeep can differ with time, relying on how the gear works. Be certain that the valve block is leak-free before the inspection. Atmosphere: Parker Hydraulics acts fastidiously, protecting the world all around so our products limit polluting something necessary to customers’ health. Merchandise: New and protected materials go into merchandise that may also be recycled, saving users money and reducing waste. Parker Hydraulics’ gear pumps have operating pressures up to 3,650 psi and speeds up to 2,000 rpm while providing superior performance which provides optimum efficiency and low noise at high working pressures. Gear pump sizes vary from 8-19cc. Screw pumps are dependable and economical low-strain pumps are free from pulsations, ensuring a protracted service life and quiet operation. Pressure relief groove special designs ensure low circulate pulsations and low noise levels.
These motors convert the pressure from hydraulic fluid stress right into a rotational motion having torque. The hydraulic fluid enters the motor by ports under stress pushing the motors shaft to create torque. They work greatest in functions having a medium circulate fee and pressure. Largely utilized in hydraulic system functions having a excessive movement charge with medium pressure. They're best fitted to purposes having a excessive pressure and stream rate. The guts of the Hydraulic System for sale is the efficient mixture of all these elements working effectively together. If you'd like to ensure a protected and environment friendly operation, carry out correct maintenance of each part. Excessive-volume flows of hydraulic fluids will probably be required to make sure fast movements during excavation. That is achieved with differential cylinders, whose hydraulic stream raters are twice the installed pump volume. An excavator’s drive system ought to convert a hundred% of the engine output hydraulically. And its hydrostatic power might be a lot increased than the utmost engine output. Every movement’s volume stream is optimized; attributable to economic causes, the number of pump circuits is proscribed, so this motion optimization is achieved by combining or separating pump circuits. For that function, independent movement is achieved by tuning the hydraulic flows via control valves, though more advanced methods make the most of and software and sensor expertise. It's the newer hydraulic management methods that are utilizing intelligent electric systems and electronics.
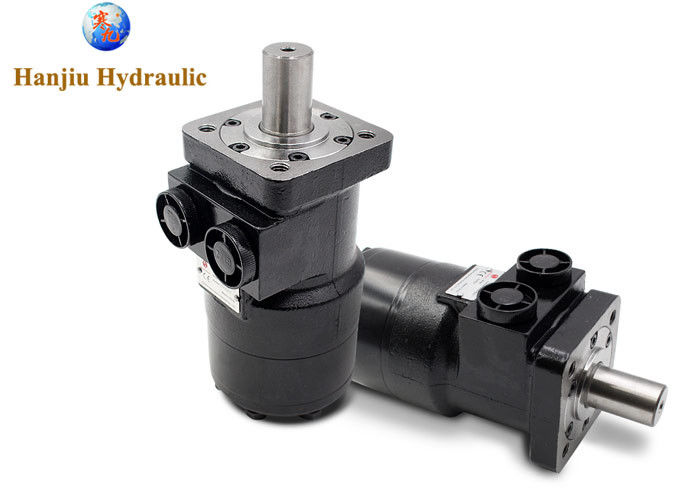
Contaminants in hydraulic fluid can include particles, dirt, steel shavings, and different debris that can injury hydraulic components, reduce efficiency, and lead to system failures. The hydraulic filter performs a crucial function in sustaining the cleanliness of the hydraulic fluid by trapping and eradicating these contaminants. The hydraulic oil could comprise various contaminates like welding scales, steel chips, tapping compound, sand particles, sludge, rust, water and dirt and so forth which may lead to put on, corrosion, poor efficiency and finally failure of the tools.
Hydraulic motors are one in every of many mechanical components that make your equipment work the best way it’s purported to. Here, we take a look at what hydraulic motors are, and why they’re important. What are Hydraulic Motors? A hydraulic motor converts hydraulic energy into mechanical energy; a rotating shaft. It uses hydraulic pressure and flows to generate the required torque and rotation. When S6 is energized, we will begin extending the cylinders in a prescribed manner. The stream will come out of work port B through a flow control valve. Since we've a positive displacement pump, we didn’t wish to have the remaining oil bypassed over the relief valve. We did this by using a compensated movement control in order that our extra flow would go right to tank (port 2) at a a lot diminished stress. The metered fluid (port 3) then goes on to a counterbalance valve the place it can free flow through the test valve. We use hydraulic directional control valves to track fluid in a system or circuit to a number of units as demanded. They shift between discrete positions equivalent to lengthen, retract, or neutral locations for controlling a hydraulic cylinder. They may also change into intermediate states to control an actuator’s acceleration, pace or direction.
- 이전글Guide To Patio Sliding Doors Repair: The Intermediate Guide On Patio Sliding Doors Repair 24.10.13
- 다음글Road Discuss: PokerTube 24.10.13
댓글목록
등록된 댓글이 없습니다.